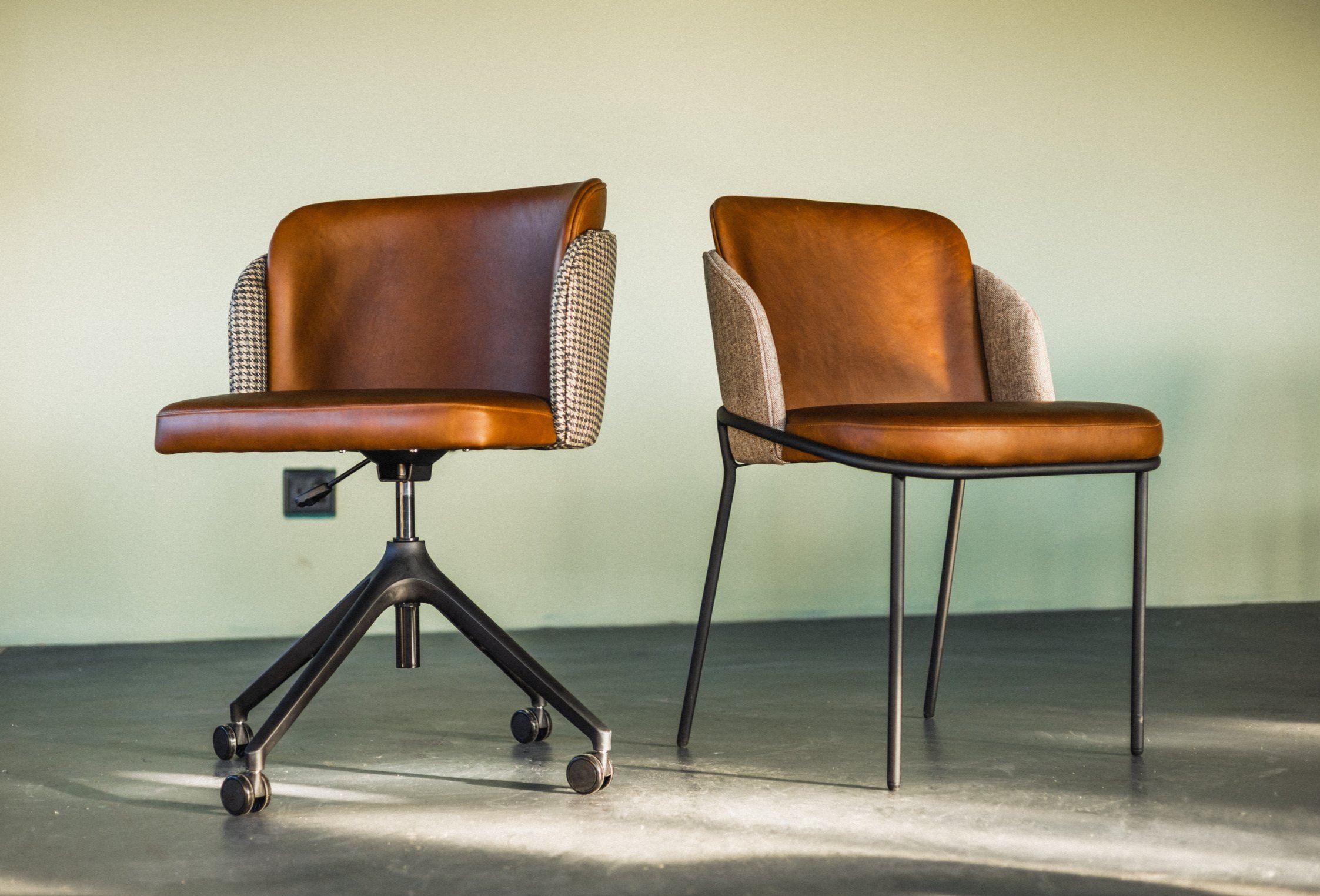
ABOUT US
COLLABORATION IS KEY
Woodlam collaborate closely with their clients on design to ensure that the final delivered product remains aesthetically pleasing to it’s natural surroundings while still meeting all exacting standards required.
Woodlam products are primarily manufactured from moulded plywood components, produced in-house, solid wood and steel frames.
The manufacture of moulded plywood involve the use of layers of thin wood veneers glued together, while formed to shape in moulds under hydraulic pressure and cured using radio-frequency and other heating methods. The process of moulding-in curves and bends eliminates many joints needed in conventional furniture assembly. In doing so, the strength of the finished product is substantially increased. After curing, the components are cut and drilled using the most modern machinery including a C.N.C (Computer Numeric Controlled) machining centre to ensure maximum possible accuracy.
THE FOUNDER
Søren Henrik Bang Lassen was born in Denmark in 1957, and moved to South Africa in 1980. He has been manufacturing furniture and moulded plywood for over 40 years.
I have come to realise what we’ve been doing for the past 40 years has much more to do with people and their lives than simply delivering well made chairs on clients’ orders. Every chair that leaves our factory has been made by hand, with the help of technology and laminating presses which date back decades to the way our Danish forefathers’ design processes.
While nothing seems to have changed everything has, because we have added our own modern South African touch to styling and production to bring products of design and relevance to the local market.
OUR STORY
For more than 34 Years, Woodlam has been at the forefront of the furniture industry designing and creating specialised furniture for the Restaurant and Hospitality Space. The Woodlam team is led by Søren Lassen. With a multitude of experience behind him, Søren and his team have pushed the limits on creating ingenious furniture that is unique, comfortable and durable.
HOW IT ALL WORKS
Most joints are secured three-way; dowelled, glued and mechanically fixed with machine screws into threaded metal cross dowels. In cases where screw fixings into wood are considered inadequate for show-wood seats or shells, use of rivets are made. A durable finish is achieved by the use of a tough reaction-type lacquer, coupled with multiple sanding stages, on all show-wood parts. All steel frames, after a seven stage cleaning and preparation process, are finished with baked epoxy powder coating. Chrome plating is optional on certain ranges subject to minimum quantities.
A wide selection of wood finishes are available, ranging form ‘blond’ to exotic timbers to a variety of stained finishes. Choice of upholstery fabrics is virtually unlimited and customers are welcome to supply fabric on a C.M.T basis.
While aesthetics and innovative design are cornerstones of the Woodlam product range, strength and durability are considered to be of paramount importance. The abundance of light-duty imported seating (primarily suited to household use only) lacks the durability which is built into Woodlam products and is essential for the rigours of contract and office applications.
Most joints are secured three-way; dowelled, glued and mechanically fixed with machine screws into threaded metal cross dowels. In cases where screw fixings into wood are considered inadequate for show-wood seats or shells, use is made of rivets. A durable finish is achieved by the use of a tough reaction-type lacquer, coupled with multiple sanding stages, on all show-wood parts. All steel frames, after a seven stage cleaning and preparation process, are finished with baked epoxy powder coating. Chrome plating is optional on certain ranges subject to minimum quantities.
A wide selection of wood finishes are available, ranging form ‘blond’ to exotic timbers to a variety of stained finishes. Choice of upholstery fabrics is virtually unlimited and customers are welcome to supply fabric on a C.M.T basis.
While aesthetics and innovative design are cornerstones of the Woodlam product range, strength and durability are considered to be of paramount importance. The abundance of light- duty imported seating (primarily suited to household use only) lacks the durability which is built into Woodlam products and is essential for the rigours of contract and office applications.
THE FACTORY
Woodlam products are primarily manufactured from moulded plywood components, produced in-house.
The manufacture of moulded plywood involve the use of layers of thin wood veneers glued together, while formed to shape in moulds under hydraulic pressure and cured using radio- frequency and other heating methods. The process of moulding-in curves and bends eliminates many joints needed in conventional furniture assembly. In doing so, the strength of the finished product is substantially increased. After curing, the components are cut and drilled using the most modern machinery including a C.N.C (Computer Numeric Controlled) machining centre to ensure maximum possible accuracy.